To invent porcelain, Europeans turned to alchemists and burned cow bones
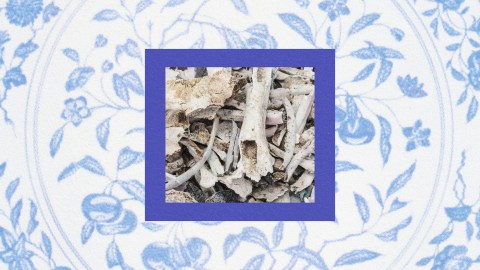
- Porcelain was developed during China’s Han dynasty (25-220 AD) after 1,500 years of experimentation with clays.
- In the early 18th century, German alchemists produced a white ceramic that closely resembled Chinese porcelain.
- Soft-paste porcelains like English bone china — first mass-produced in the late 18th century — are still used today for British afternoon tea.
The story of the “china cup” began around 2,000 years ago, in China. Porcelain as we’d recognize it today was developed during the Han dynasty (25-220 AD) following early experimentation with porcelain-like clays in the 1,500 years leading up to this period. At this time and over following centuries, all sorts of ceramic goods were in high demand in both China and across the Islamic world. Early craftspeople honed their skills for producing pottery in answer to this need, but all was done on a small, local scale.
Around 1000 AD, the Chinese porcelain makers got organized, and production became centralized around a town called Jingdezhen. This was thanks to its notably tall (kow or gao) hill (ling), out of which was extracted the crucial clay ingredient, kaolin (pronounced “kay-lin,” after the tall hill kow ling). Porcelain goods were produced here on a mammoth scale; the kilns at Jingdezhen could fire up to 25,000 objects at a time. This saw the town become the main producer of porcelain for the next 900 years.
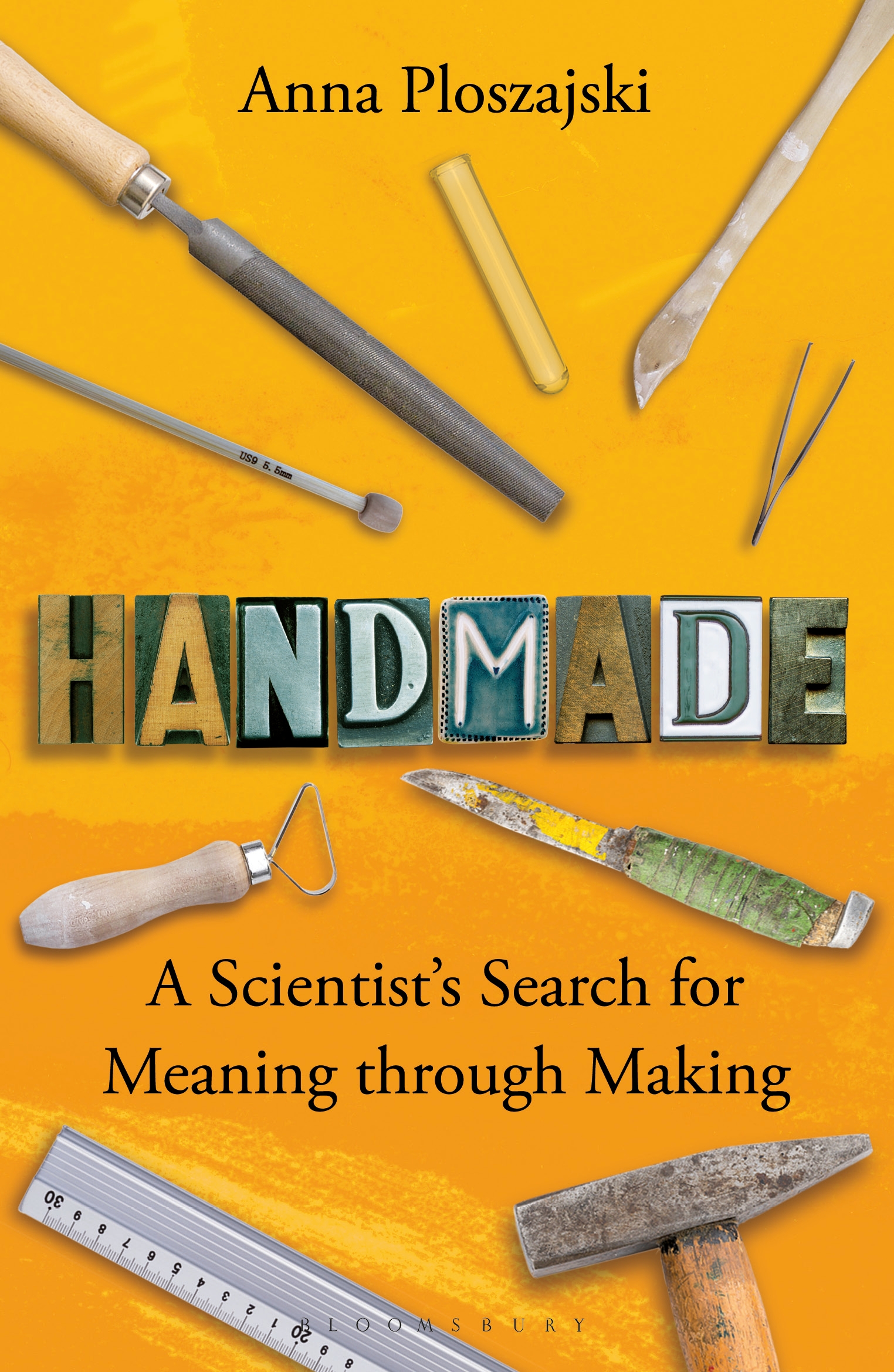
During the Ming dynasty (1368-1644 AD), trade along the Silk Road to the west and the Tea Horse Road to the southwest, as well as exports across the seas, saw porcelain wares — and Chinese ideas and culture — diffuse across Asia, Africa, and Europe. Such commerce brought about new materials and designs, like the blue cobalt pigments from Iran that were used on Chinese porcelain to create the blue and white wares with which we are still familiar today.
Despite the mammoth scale of production in Jingdezhen, porcelain exports were tightly controlled. But the Europeans’ taste for the stuff was insatiable, and with a limited supply of porcelain wares coming into Europe, they turned their sights towards discovering the Chinese’s secret. For years they toiled without success but eventually, around 1708, German alchemists Johann Friedrich Böttger and Ehrenfried Walther von Tschirnhaus managed to produce a hard, white, translucent ceramic that closely resembled Chinese porcelain. The Germans didn’t mess around; a factory immediately popped up at Meissen in eastern Germany to meet European demand for porcelain, and they kept their recipe a jealously guarded secret.
Meanwhile, exasperated by all this secrecy, the French took the approach of just going to China and asking them how to do it. François Xavier d’Entrecolles was a Jesuit priest working in Jingdezhen who observed the kilns, interviewed some of his new Chinese religious converts, and happened to catch a glimpse of the written specifications of how to make the so-called white gold. He wrote home relaying tales of his discovery.
Despite gaining the secret of the Chinese method, all of the earlier European experimentation didn’t turn out to have been a complete waste of time. Porcelain from the Meissen factory produced a similar material to the Chinese stuff, known as hard-paste porcelain, but a whole new type of porcelain called — hold on to your saucers — soft-paste porcelain was also developed in the search for the secret. Even within soft-paste porcelain, the Italians, the French, and the English had all developed their own unique formulae for mimicking the Chinese material, involving different ingredients and firing treatments.
You know what they say: If you can’t bring the kaolin mountain to Essex, burn all the cows.
In the 1740s, two soft-paste porcelain factories were founded in England: the Chelsea Porcelain Manufactory and the Bow Porcelain Factory. The latter was located near the cattle markets and slaughterhouses of Essex, which, gruesomely, provided them with a large supply of bone ash, which is exactly what it sounds like. You know what they say, if you can’t bring the kaolin mountain to Essex, burn all the cows.
Thomas Frye, the founder at Bow, patented the use of this unusual ingredient in porcelain in 1748. Josiah Spode of Stoke-on-Trent later improved the process and marketed the product as “bone china,” and soon bitter rivalries sprung up between all the English pottery manufacturers, each suspicious of the others’ recipes. On one occasion, a desperate founding partner from the Lowestoft Porcelain Factory reportedly stowed themselves away in a barrel, in a frantic attempt to spy on the mixing of ingredients by their rivals at Bow.
Eventually, in 1771, French nobleman Nicolas-Christiern de Thy published L’art de la Porcelaine (The Art of Porcelain), featuring the detailed production process of the Chinese recipe. However, by this time the Europeans seem to have decided that having gone to all this effort of developing their own processes, they actually quite liked their versions after all. Soft-paste porcelains like English bone china were a roaring success, and to this day still form the centerpiece of any quintessentially British afternoon tea worth its scones.