To build a circular economy, we need to put recycling in the bin
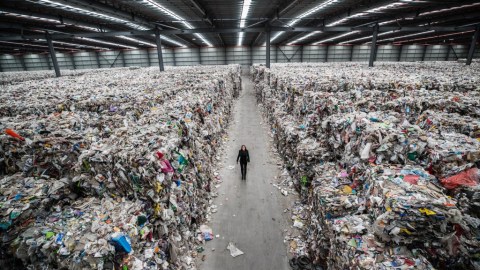
Jason South/The Age via Getty Images
Too often the concept of a circular economy is muddled up with some kind of advanced recycling process that would mean keeping our industrial system as it is and preserving a growing consumption model.
This idea is based on a belief that recycling will take care of everything.
One of the most startling examples of this is the part of the European Union’s Circular Economy Action Plan which aims to increase recycling rates: up to 70% of all packaging waste by 2030 and 65% of all municipal waste by 2035. In a properly built circular economy, one should rather focus on avoiding the recycling stage at all costs. It may sound straightforward, but preventing waste from being created in the first place is the only realistic strategy.
While we obviously need to continue recycling for quite some time, putting the emphasis on genuine circular innovations – that is, moving us away from a waste-based model – should be our sole objective.
Recycling is linear
In a linear economy, we do not account for the side-effects generated by a product once sold to an end customer. The aim is to sell a maximum number of products at minimal cost. Continuous pressure to reduce costs leads to the creation of many of these side-effects – called externalities by economists. The higher a company’s rate of production and the higher its efficiency, the more successful it will be at selling its goods in a fiercely competitive environment.
What is a circular economy?
This worked well in the 20th century when resources were easily available and raw material prices kept decreasing. Waste, as an economic externality, was not the producers’ responsibility. Managing waste cycles, dumping it out of sight or, at best, recycling it – but only when it was cost-effective – were under the control of our national institutions.
Visionary manufacturers, who understand the upcoming challenges of increasing their economic resilience, know better: a product that is returned for repair will cost less to fix and sell again, than manufacturing it from scratch.
In our current model, we extract resources, transform them into products, and consume or use them, prior to disposing of them. Recycling only starts at the throwing-away stage: this is a process that is not made to preserve or increase value nor to enhance materials.
We need to understand that recycling is not an effective strategy for dealing with unused resource volumes in a growth model. We will find ourselves in a never-ending pursuit of continuously generated waste, rather than seeing the avoidance of waste as a path to beneficial innovations on many levels.
Of course, it is easier to think about recycling. This avoids changing the whole of our volume-based production model. But in a world where we have to shift our consumption patterns and use less energy, recycling no longer has all the answers.
Recycling is ‘business-as-usual’
Since we cannot stop the volume of waste overnight, investments in the recycling industry are needed. But truly meaningful investment in developing a circular economy takes place outside of the recycling space. Indeed, the more we recycle and the more we finance recycling factories, the more we stay ‘linear’. We mistakenly believe this is the best route to solve our problems – but by staying in a recycling-based economy, we will delay the transition to an advanced circular economy.
In a circular economy, resources do not end up as recyclables since products are made to last several lifecycles. Products’ lifespans are extended via maintain, repair, redistribute, refurbishment and/or re-manufacture loops, thus they never end up in the low-value, high-need-for-energy loop: recycling.
We live in a world in dire need of disruptive innovations. Closing loops next to where customers live while avoiding waste is a short and longer-term win-win for any leading re-manufacturer. Short-term because you are in direct contact with your customers, and taking back a product that needs maintenance is an opportunity to better understand their needs and help them with additional services. Long-term because you will lower your exposure to future financial risks. Any of the feedback loops that exist prior to the recycling loop are an opportunity to take back control over your stock of resources – taking control away from the raw material markets, which may become highly volatile. Increased interactions with your customers, both commercial and financial, and an in-depth understanding of their needs, would increase customer loyalty and a business’ overall resilience.
Re-using, re-distributing and/or remanufacturing strategies are the preferred approaches in a circular economy, as they are based on parts durability. Caring for and preserving the value of product components increases corporate economic resilience, while diminishing external market risks. Whether you are acting in a highly advanced or a developing economy, these strategies make crystal-clear sense: they are less costly in the long-run because repairing a product made to last is always less expensive than producing it from scratch.
Leapfrogging into valued supply chains
Following this approach, we must move away from activities that devalue the material, such as recycling, and instead invest in those activities that preserve it: reuse and remanufacture. These two are especially important since they create many more secure jobs. Walter R. Stahel, the godfather of the modern circular economy, introduced the metric of labor input-per-weight ratio (man-hour-per-kg, or mh/kg) to measure job creation in relation to resource consumption. He found that the ratio of mh/kg when building a remanufactured engine from used resources compared to making the same engine from virgin materials is 270:1. The impact on employment is huge.
The re-localization and the re-sizing of activities closer to customers become critical. Production sites should migrate from a highly centralized global hub to units designed to fulfill local needs. In developed markets, a possible plan could be to develop strategic partnerships with local service providers, who can provide the infrastructure. In emerging markets, where there is often an urgent need for jobs, leapfrogging straight into a national re-manufacturing strategy is the way forward. Becoming the next ‘world factory’ hub is an obsolete vision today.
One way to start thinking like a leader in the next economy while creating jobs could be in order of priority:
- Reuse by repairing (goods) through re-hiring (people), while sharing the radical benefits (awareness) of such a model
- Redistribute by promoting access (goods) through collaboration (people), while sharing information (awareness) about this model
- Remanufacture via the ease of disassembly (goods) by training (people), while sharing the acquired knowledge (awareness) through this model
- Migration of recycling activities by diverting (goods) to service models, transferring skills (people) to remanufacturing processes (awareness).
All of the above make sense in a world where planetary limits have already hit most economies.
Adopting a circular strategy by avoiding reliance on recycling is the way forward.
This is about genuine innovation derived from genuine leadership.
Reprinted with permission of the World Economic Forum. Read the original article.