“Iron Man” material made from DNA and glass is 4x stronger than steel
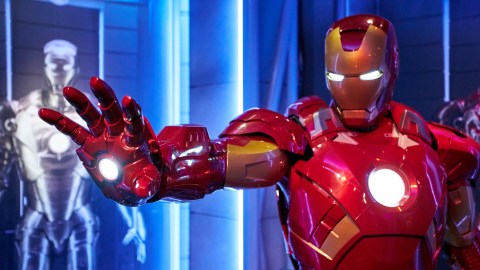
- Science fiction inspires real scientific advances, like a new material inspired by Iron Man, which is made from glass and DNA and is four times stronger and five times lighter than steel.
- The material is crafted using "DNA origami" to create a lattice structure and then coated with silica glass.
- Despite its potential, the material faces production challenges and requires further research to refine and enhance its properties for practical use.
One of the cool things about science fiction is that it can inspire real science and innovation. Jules Verne’s 20,000 Leagues Under the Sea emboldened underwater exploration. William Gibson’s Neuromancer influenced the development of the internet, while Neal Stephenson’s Snow Crash popularized the concept of the metaverse. Douglas Adams’s Hitchhiker’s Guide to the Galaxy introduced the idea of e-books — in addition to giving us the answer to life, the universe, and everything.
Who knows what other real advances science fiction will successfully inspire? Flying cars? Space cities? Iron Man suits?
Actually, that last one has already spurred a breakthrough. Researchers from Columbia University, Brookhaven National Lab, and the University of Connecticut recently assembled a team to see if they could create a material worthy of Tony Stark. What they developed was a material four times stronger than steel and five times lighter. And they made it using only glass — and DNA.
DNA, assemble!
Lightweight materials are sought after by engineers for their ability to reduce manufacturing costs while improving performance and efficiency. Strong materials are also valued because they hold up the stresses of mechanical use.
Finding materials that balance those qualities can allow for a wide range of applications and improvements. A lighter car, for instance, can travel farther while using less fuel than a heavier one, but it still needs to be sturdy enough to be safe. Unfortunately, strength and slightness are often at odds. Stronger materials tend to be heavier and lighter ones less durable.
Compounding the problem is manufacturing. Large-scale production can introduce flaws and imperfections into materials with a complex molecular structure. Glass is a perfect example. We consider glass to be fragile because it shatters so easily; however, this is due to flaws and impurities, such as micro cracks or missing atoms. A flawless cubic centimeter of glass, the researchers note, could “withstand 10 tons of pressure.”
“I am a big fan of Iron Man movies, and I have always wondered how to create better armor for Iron Man. It must be very light for him to fly faster. It must be very strong to protect him from enemies’ attacks,” Oleg Gang, study author and nanomaterials scientist at Columbia, said.
To ensure fewer flaws, the team decided to construct their new material at the nanoscale. This way, they could have more control over the delicate molecular arrangement. But first, they needed a framework on which to arrange the molecules, and their scaffold of choice was DNA.
DNA has several advantages for construction at this tiny scale. To start, it already exists in nature and is widely available. It is also a polymer made up of monomers (called nucleotides). This makes DNA a resilient and elastic material — much like the everyday synthetic polymers rubber and polyester. And these properties make it sturdy framing for building nanostructures.

To construct the frames, the team used a technique known as “DNA origami,” named after the Japanese art of paper folding. They combined large strands of DNA (called “scaffolding strands”) with short strands (called “staple strands”) in a liquid solution. These staple strands bind to the scaffold strands at specific locations. Once attached, they fold the scaffold strand, and like its artistic namesake, these folds eventually add up to a desired shape. In this case an octahedron (a 3D shape kind of like two pyramids stuck together). The octahedrons further bind to each other at their points to create a repeating pattern known as a lattice.
One more advantage: DNA is self-assembling. Hydrogen bonding ensures the DNA bases of the scaffolding and staple strands will be drawn together. The researchers simply need to heat up and anneal the solution, and voila: DNA lattices! “We focused on using DNA as a programmable nanomaterial to form a complex 3D scaffold, and we wanted to explore how this scaffold will perform mechanically when transferred into more stable solid-state materials,” Aaron Michelson, the study’s lead author and a postdoctoral researcher at Brookhaven, said.
A nano-stress test
The researchers next coated the DNA lattices in a thin layer of silica glass. The glass layer was only about 5 nanometers thin or — depending on how you look at it — a few hundred atoms thick. To keep the material ultra-lightweight, they chose not to fill the lattices’ inner spaces.
“We were very interested to explore how we can enhance mechanical properties of regular materials, like glass, by structuring them at the nanoscale,” Gang added.
Of course, at this scale, it was impossible to test the new material’s properties through conventional methods like a universal testing machine. The researchers instead opted for a technique called nanoindentation. Essentially, a small probe applied pressure to the DNA-glass material while an electron microscope allowed the researchers to measure its behavior. Their testing revealed that the material could reach a yield strength of between 1-5 gigapascals (a unit of pressure worth one billion pascals). For comparison, gigapascals are typically used by geologists to measure the immense pressure within the Earth’s mantle.
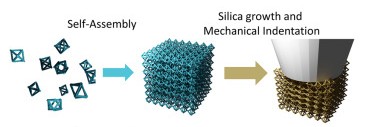
“Our new material is five times lighter but four times stronger than steel. So, our glass nanolattices would be much better than any other structural materials to create an improved armor for Iron Man,” Gang said.
Seok-Woo Lee, study author and a materials scientist at the University of Connecticut, added: “For the given density, our material is the strongest known.”The team published their findings in Cell Reports Physical Science, a peer-reviewed, open-source journal from Cell Press.
The ability to create designed 3D framework nanomaterials using DNA and mineralize them opens enormous opportunities for engineering mechanical properties.
Oleg Gang
Time to suit up?
With that said, it may be a while before you can start building an Iron Man suit with this material. The researchers found that the larger lattices were more prone to defects. The most common were voids and vacancies in the structures that caused them to lose strength. Additionally, buffer solutions used to keep the DNA stable had the potential to add impurities such as carbon, phosphorus, and nitrogen into the mix.
“The ability to create designed 3D framework nanomaterials using DNA and mineralize them opens enormous opportunities for engineering mechanical properties. But much research work is still needed before we can employ it as a technology,” Gang said.
Looking ahead, the team wants to see if they can create an even stronger material using these techniques. One possibility is to construct nanostructures using different lattice configurations. Another is to coat the lattices in a different material, such as carbide ceramics.
Even if these nanostructures never scale to Iron Man — or even Ant-Man — size, nanostructures still have the potential to help us build future technologies or improve current ones, such as superconductors and battery cathodes. Another win for the partnership between science and science fiction.
This article was originally published by our sister site, Freethink.