3D-printed “metamaterial” is stronger than anything in nature
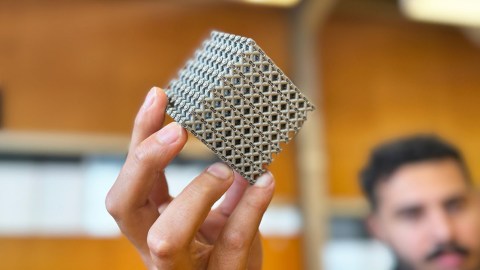
- A “metamaterial” is a material with properties not seen in nature.
- Researchers used 3D printing to create a metamaterial with a lattice structure that distributes load stress more evenly.
- It proved to be 50% stronger than the strongest alloy of similar density used in aerospace.
Using lasers and metal powder, Australian scientists have created a super strong, super lightweight new “metamaterial” — but they got the idea for this sci fi-sounding creation from plants.
The challenge: Materials that are strong yet lightweight, such as carbon fiber and graphene, are used to make everything from medical implants to airships, and developing ones with ever greater “strength-to-weight ratios” is the goal of many material scientists.
In pursuit of that goal, some have turned to nature, looking for ways to replicate in metal the hollow lattice structures, like those in the Victoria water lily, that make some plants remarkably strong.
“These two elements together show strength and lightness never before seen together in nature.”
Ma Qian
What they’ve been able to create so far using available manufacturing techniques have fallen short, though — an uneven distribution of load stress is a major reason these synthetic materials don’t turn out as strong as their natural counterparts.
“Ideally, the stress in all complex cellular materials should be evenly spread,” said Ma Qian, a distinguished professor of advanced manufacturing and materials at RMIT University. “For most topologies, it is common for less than half of the material to mainly bear the compressive load, while the larger volume of material is structurally insignificant.”
What’s new? Using an advanced metal 3D-printing technique, Qian’s team has now created a new “metamaterial” — a material with properties not seen in nature — with a lattice structure that distributes load stress more evenly.
In testing, their metamaterial, fabricated from a common titanium alloy, proved to be 50% stronger than the strongest alloy of similar density used in aerospace.
“We designed a hollow tubular lattice structure that has a thin band running inside it,” said Qian. “These two elements together show strength and lightness never before seen together in nature. By effectively merging two complementary lattice structures to evenly distribute stress, we avoid the weak points where stress normally concentrates.”
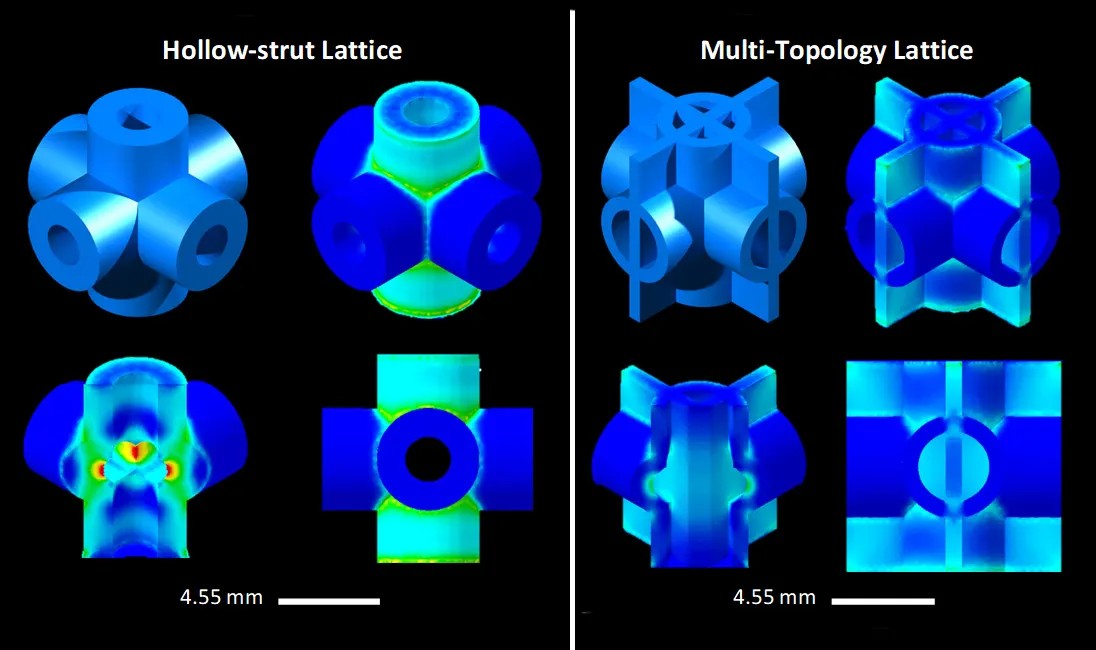
Making a metamaterial: To create their super strong metamaterial, the RMIT team relied on a 3D printing technique called “laser powder bed fusion,” which is very different from traditional 3D printing, where a material is extruded from a nozzle layer by layer.
Instead, a layer of metal powder is spread over the base of the printer. A laser is then used to melt the powder in the desired pattern. Another layer of powder is then added to the bed, and the process is repeated, with the newly melted metal binding to the metal below it.
Looking ahead: While this technique enabled the creation of the unique metamaterial, it could also be a hurdle to getting it out of the lab and into real-world applications — at least initially.
“Traditional manufacturing processes are not practical for the fabrication of these intricate metal metamaterials, and not everyone has a laser powder bed fusion machine in their warehouse,” said lead author Jordan Noronha.
“However, as the technology develops, it will become more accessible and the printing process will become much faster, enabling a larger audience to implement our high-strength multi-topology metamaterials in their components,” he continued.
This article was originally published by our sister site, Freethink.